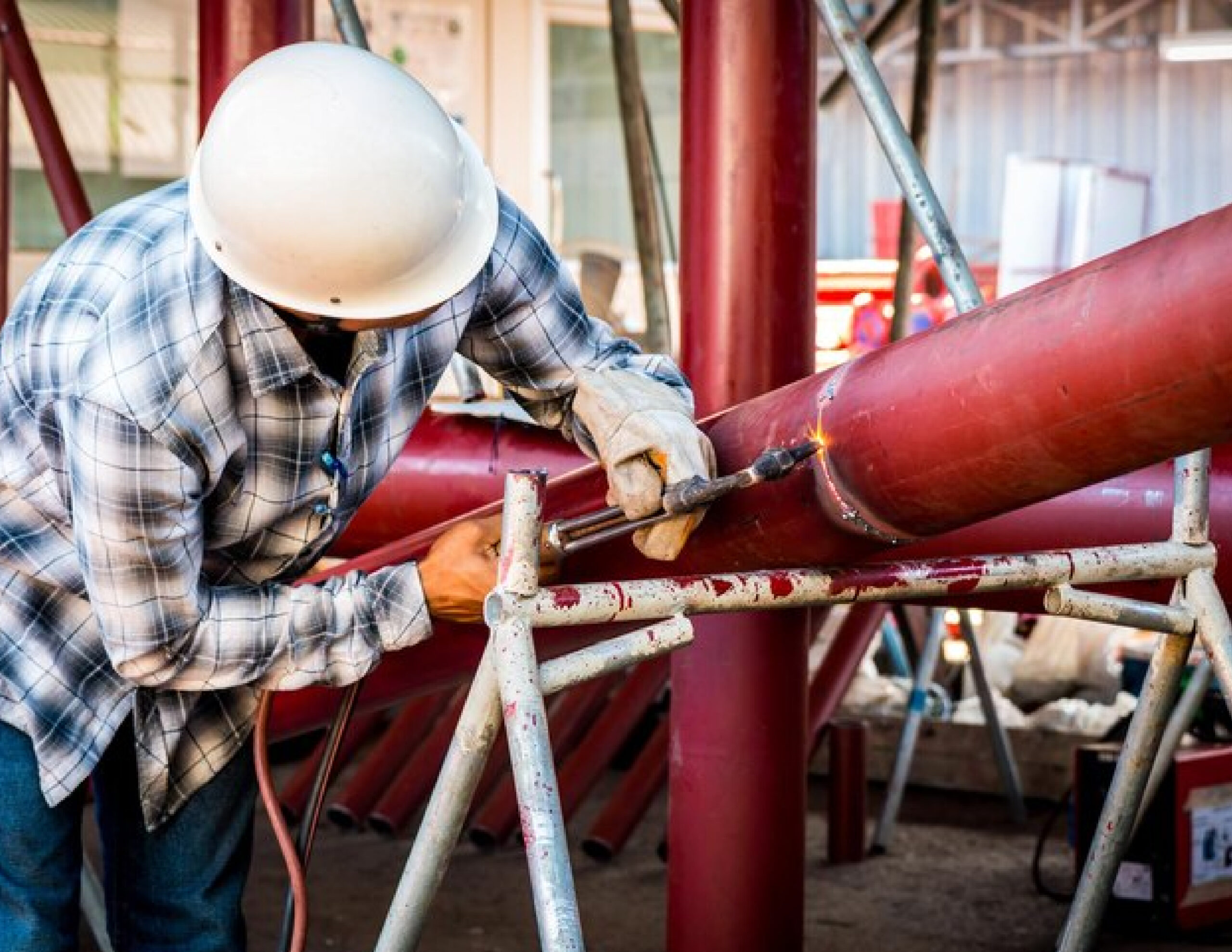
About Course
The 3G uphill welding position is an essential technique used for welding plates set in a vertical position. In this configuration, the welder moves the arc or torch upward along the joint, which presents a specific set of challenges due to gravity and heat control. This welding position is crucial in industries such as shipbuilding, construction, and heavy equipment manufacturing, where structural strength and precision are paramount.
Materials Specification: 12mm Thick Plate
- Plate Thickness: 12mm
- Material Type: Usually carbon steel, mild steel, or alloy steel. The exact material depends on the project, but 12mm thick plates are common in structural applications.
- Joint Configuration: The plates are typically prepared with a beveled edge for proper penetration and welding bead buildup. A single-V or double-V groove is common.
Welding Processes Used in 3G Uphill
The module involves the use of two welding processes for this position: MMAW (Manual Metal Arc Welding) and GMAW (Gas Metal Arc Welding).
1. MMAW (Manual Metal Arc Welding) Module
Also known as Shielded Metal Arc Welding (SMAW) or Stick Welding
Key Elements:
- Electrode Type: Consumable, such as E7018 for structural applications or E6010 for open root passes.
- Polarity: DC Electrode Positive (DCEP) for better penetration and arc stability.
- Amperage Setting: Between 90-140A depending on the electrode size (2.5mm, 3.2mm, or 4mm) and thickness of the plate.
- Welding Technique:
- Root Pass: A stringer bead technique is typically used with slight oscillation, ensuring proper penetration and avoiding undercut.
- Fill and Cap Passes: A weaving technique or controlled side-to-side motion is used to control the molten pool and distribute heat evenly.
- Positioning: Uphill welding requires a steady hand, as gravity causes the molten metal to sag, which makes managing the weld pool critical.
Common Issues:
- Slag inclusion due to improper cleaning between passes.
- Undercutting or poor penetration due to improper heat control.
- Spatter due to an unstable arc or incorrect electrode angle.
2. GMAW (Gas Metal Arc Welding) Module
Also known as MIG/MAG Welding
Key Elements:
- Wire Type: Solid wire, ER70S-6 is typically used for mild steel applications.
- Shielding Gas: A mixture of argon and CO₂ (commonly 75% Ar, 25% CO₂), which provides a stable arc and protects the weld pool from oxidation.
- Polarity: DCEP (Direct Current Electrode Positive) for deeper penetration and more stable arc.
- Wire Diameter: Typically 0.9mm to 1.2mm, depending on the application.
- Voltage: Set between 18-24V based on the material and wire diameter.
- Wire Feed Speed: Typically set between 200-300 IPM (inches per minute), adjusted according to the required heat input.
Welding Technique:
- Stringer or Weave Bead: For the root pass, a stringer bead with minimal movement is used to ensure solid penetration. For the fill and cap passes, a weaving motion may be used to cover more area and ensure an even distribution of the weld metal.
- Torch Angle: Held at a 10-15 degree push or pull angle for uphill welding. This helps control the weld pool and maintain a smooth weld bead.
- Travel Speed: The speed is slower for uphill welding compared to other positions to ensure better control of the weld pool and to avoid sagging.
Common Issues:
- Porosity caused by improper shielding gas flow or contaminants.
- Lack of fusion due to poor technique or incorrect settings.
- Excessive spatter if the wire feed speed or voltage is not well-balanced.
Course Content
Study
-
Lesson
00:00